LRTM
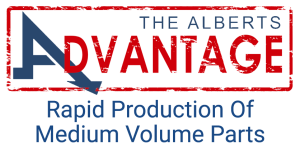
Light Resin Transfer Molding
Attributes
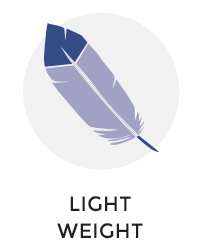
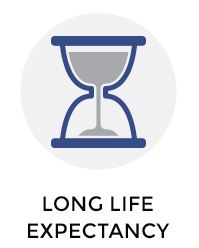
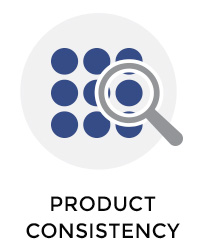
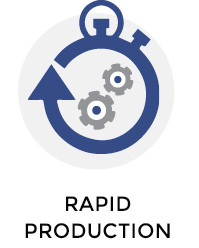
Creative Strategy
Size & Complexity
- Maximum 10’ x 10’
- Considerations: hardware, parting lines and substrates
Materials
- Resin surface coat, layers of fiberglass mat and vacuum infused or pressure pumped resin
- Considerations: compression strength, corrosion resistance, flexural, service temperature and tensile
Color Chart: Click Here
Draft
Amount of taper for molded or cast parts perpendicular to the parting line. An angle is incorporated into a wall of a mold so that the opening of the cavity is wider than its base. Draft angles allow for easier ejection of the part from the mold.- Smooth Texture: 0° draft acceptable in some cases, 1° draft preferred minimum
- Light Texture: 2° draft preferred minimum
- Heavy Texture: 3° draft preferred minimum
Wall Thickness and Radius
- Minimum .0625”
- Maximum .500”
- Preferred minimum corner radius .250”
Surface Finish
With a closed mold process, the tool side and non-tool side can capture a smooth, polished finish. The gel coat’s cosmetic finish may reveal the fabric print without a barrier coat.Tolerances
Allowable variation for any given size in order to achieve proper function when considering the design intent. As with all molded products, part material’s shrink value should be considered when building your pattern and mold.- Tool side ±.010”
- Non-tool side ±.020”